How one man took a challenge and strummed himself into a self-taught, world-renowned luthier
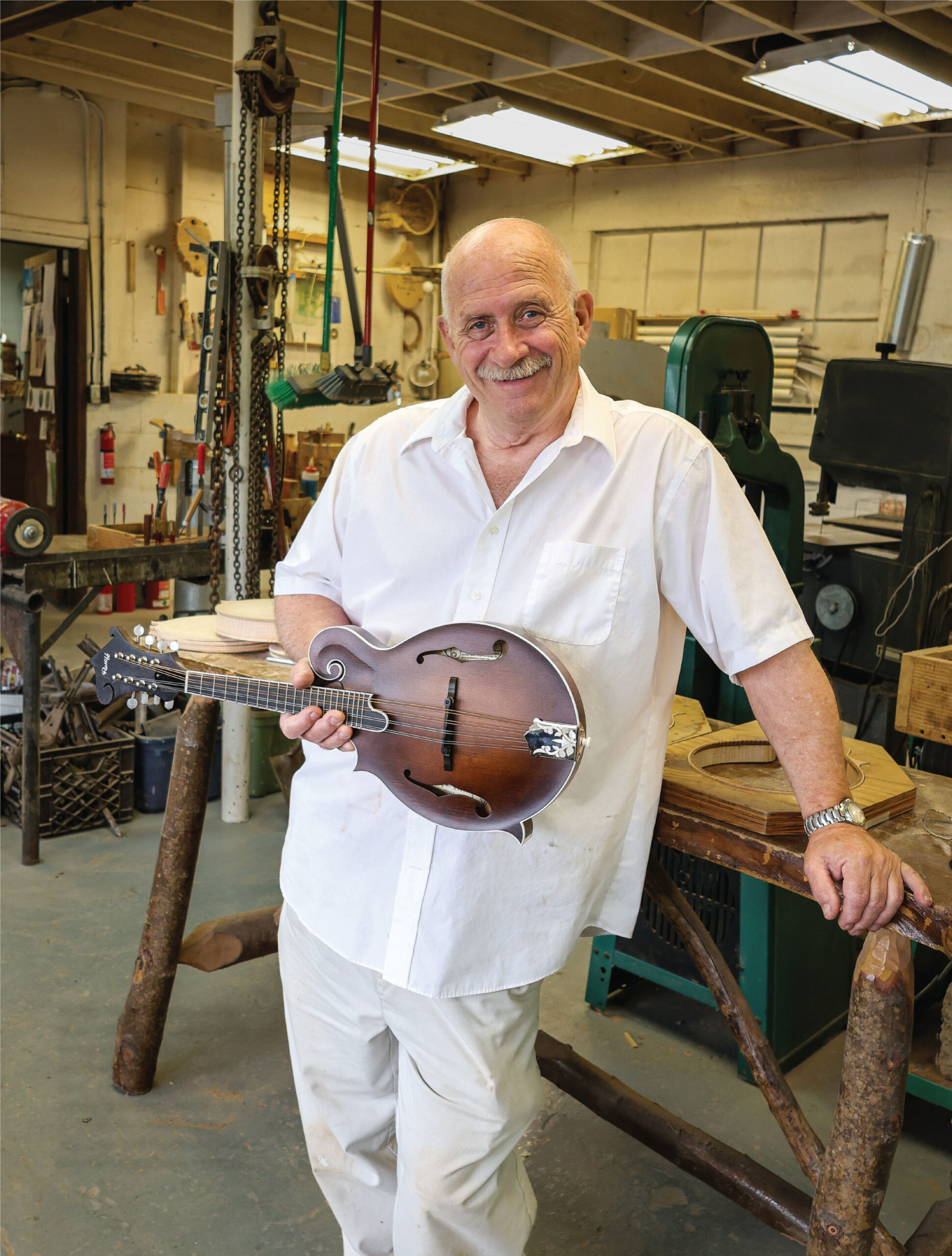
Few in life are able to discover a passion, turn it into a hobby and then make more than a four-decade career out of the same craft — but Audey Ratliff has done just that. Since 1982, Ratliff has handmade more than 1,200 mandolins in the foothills of the Great Smoky Mountains, and those time-honored traditions of the South can be found all over the world.
“You’ve heard the saying, ‘If you like what you do, then you’ll never work a day in your life’,” Ratliff shared. “Well, I’m one of those fortunate guys. I’ve never worked a day in my life doing this, and that’s the truth.”
From strumming to a purpose
Ratliff was born in Portsmouth, Virginia, but spent his childhood traveling the nation. His father worked for the Federal Aviation Administration, and that led them to various stays in the Southeast as well as ventures in Alaska and Panama. While many things changed as the Ratliffs moved, music was always a constant. His father, Tom, was a talented Dobro player and shared that zeal with his son.
“My earliest musical memory is being carried backstage on my father’s shoulders to meet Uncle Josh Graves at a Flatt and Scruggs concert in the early 1960s,” Ratliff said.
When he was 12 years old, the family made their way back to the Appalachian Mountains, and Church Hill, served by Holston Electric Cooperative, has been home ever since. From that time on, Ratliff spent his time playing the guitar in several bands. One opening for a mandolin player in his dad’s band changed the course of his life forever.
“I didn’t really know how to play, but I borrowed a teardrop mandolin from a friend,” Ratliff recalled. “I turned the strings over to make it left-handed. One of the guys in the band knew enough to teach me the songs on the set list that we had. So, I didn’t know how to play anything except for those songs.”
After a few shows, Ratliff wanted to return the borrowed mandolin and find one of his own. Being a lefty, this was easier said than done, though, as many instruments, especially mandolins, are built for right-handed musicians. He soon found a man in Virginia who was up for the unique challenge.
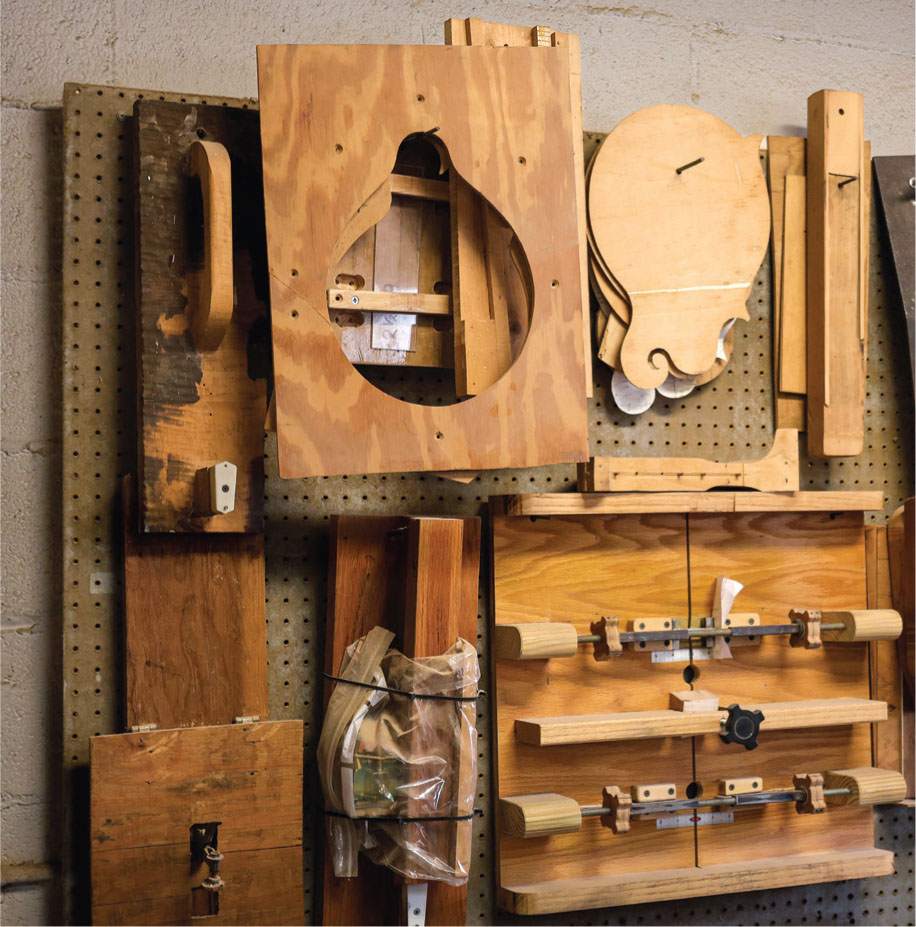
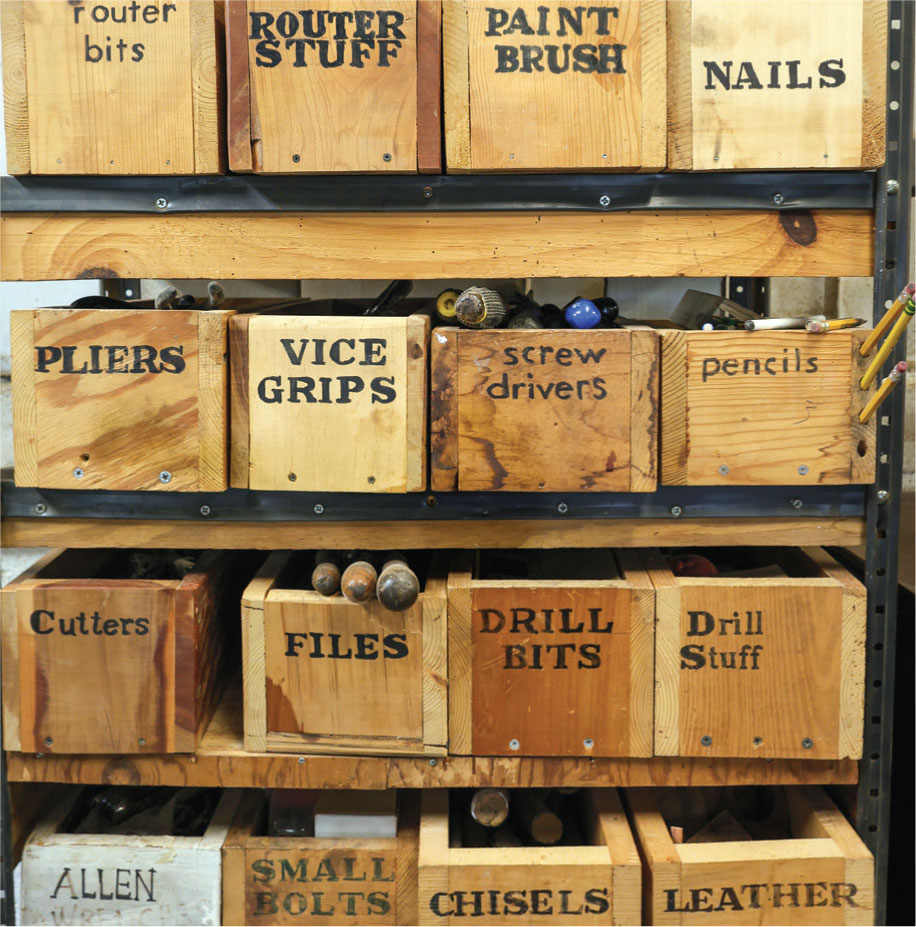
“I can remember it like it was yesterday,” Ratliff said about meeting the luthier. “It was a little old country store, and you had to shove the door open and push the sawdust out of the way. It was a step back in time, but he built a wonderful instrument.”
Ratliff played that instrument for years, and that interaction inspired him to have many more “left-handed mandolin man” conversations. But now he’s the one building the treasures.
A passion turned into a business
Ratliff’s curiosity was peaked after that connection. He began studying and learning how to make stringed instruments. Soon enough, he was creating a space in his spare bedroom so that he, too, could make both right- and left-handed mandolins.
“That man in Virginia got me interested in the process,” Ratliff said. “I bought some books on guitar, fiddle and mandolin building. I then built one and sold it. Built another and sold it. And here I am 43 years later.”
It didn’t take long for Ratliff Mandolins to outgrow the extra bedroom. He built a small shop out behind the house to continue his work. In 1994, he moved to the building he has today off Main Street in Church Hill to fulfill a contract for a warehouse distributing company. He hired seven employees to help him complete the 500-instrument job, instructing each one about the craftsmanship of making the bluegrass staple. Several of those men even went on to become prominent luthiers themselves.
All about the craftsmanship
As you can imagine, a lot of attention, time and skill go into making a fretted, stringed musical instrument. It takes Ratliff around 100 man-hours to build one single mandolin with eight strings arranged in four courses.
He generally makes two different styles of mandolins: A-style and F-style. Through those two styles are endless customizable opportunities. Ratliff considers his RA-5 “Master Model” to have all the features of the finest instruments of the golden age of lutherie. Those mandolins are bound all over with three-ply binding, genuine mother-of-pearl inlays, ebony bridge and fingerboard and top-quality hardware. His “Country Boy” mandolins include white binding around the top, ebony bridge, genuine bone nut and a satin finish. They are still high quality, just without the fancy embellishments.
In the beginning, Ratliff would create 10 custom mandolins in a batch. Each instrument still goes through the same general steps. First, he plans and designs, meaning Ratliff gathers the wood and molds he needs to make either the teardrop-shaped instrument or the more ornate, fancier style. He prepares the body by bending the sides and placing them in the appropriate molds. Then, he carves the top and back out and glues the two mirror-image pieces of wood onto the sides with spruce on the front and maple on the back. Sound holes, either F-holes or oval holes, are cut, and after some cleanup, the neck of the instrument is built and attached. Ratliff then installs binding and the fingerboard and does custom inlay. From there, he does the final sanding and applies the finish. The mandolins are then left to cure for several weeks before hardware and strings are installed. The last step is to attach the decorative tailpiece cover, and each one is hand engraved.
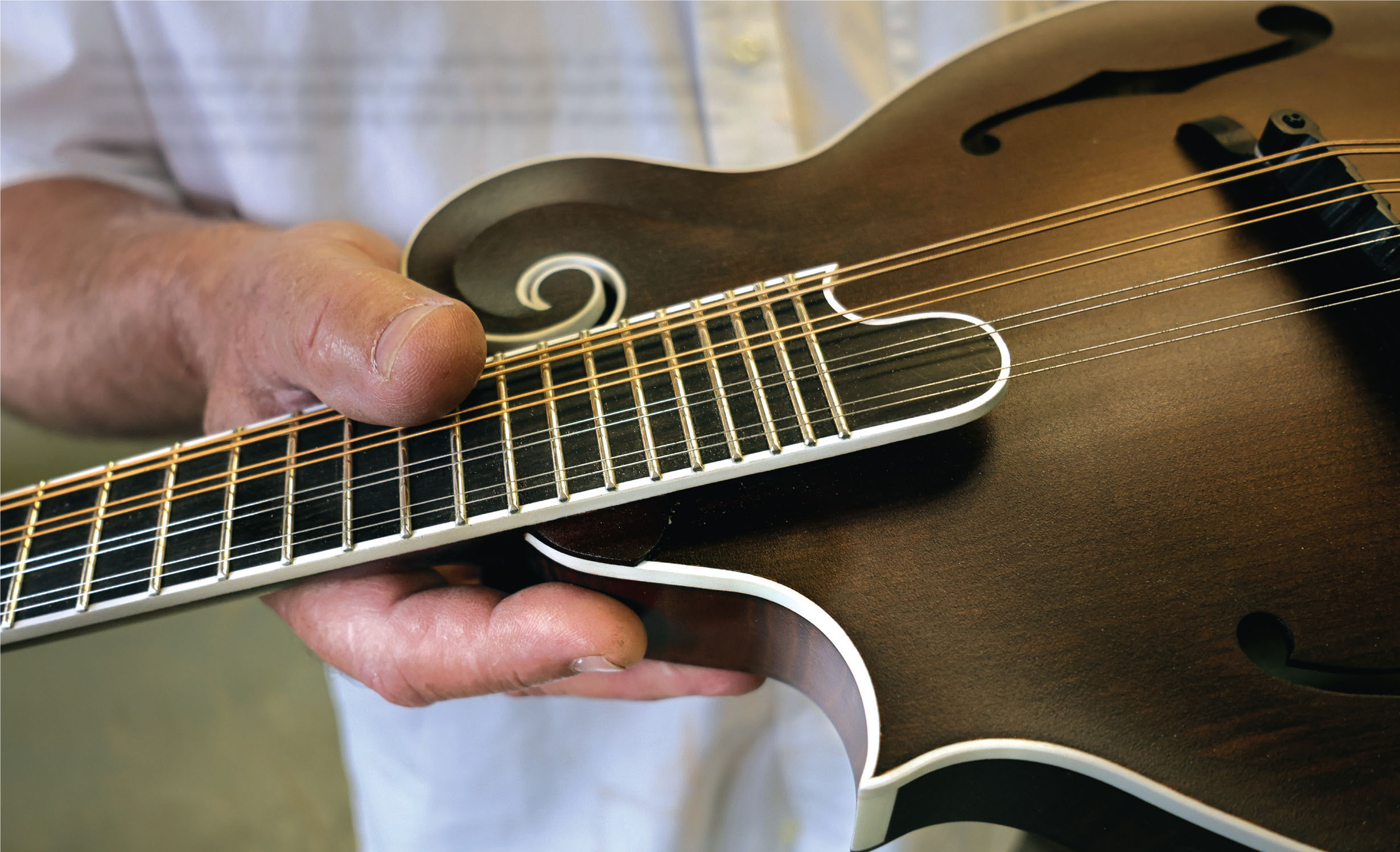
“I think I may have practiced on 1,000 pennies and quarters when I was learning how to engrave,” Ratliff said.
While the process is tedious, Ratliff enjoys sharing the steps with others and has even put together a YouTube channel demonstrating it. He posted his first videos almost 20 years ago. For a period of time, he did a weekly production diary showing every step that goes into the construction.
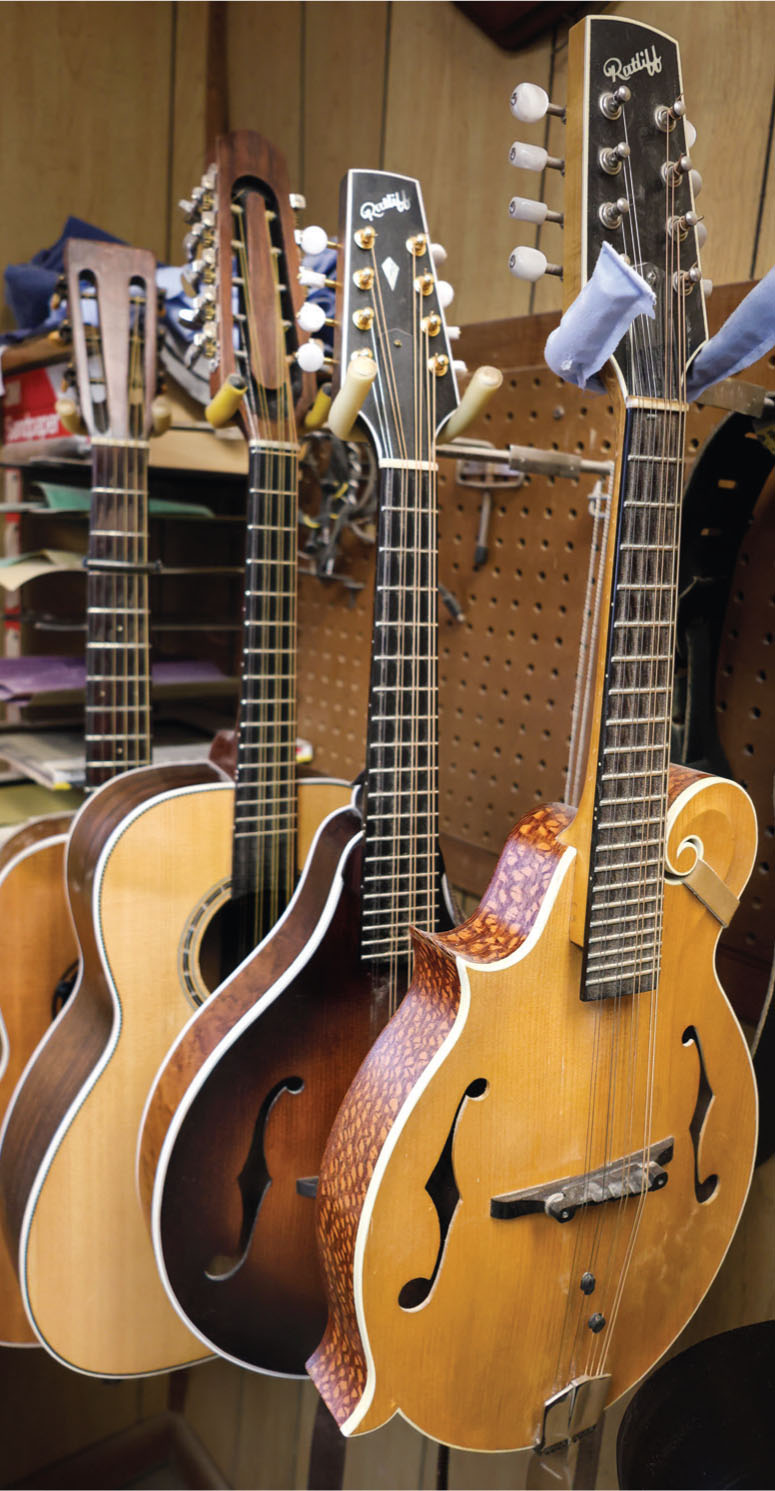
“I could tell a customer that their mandolin was No. 3 in my batch,” Ratliff said. “That way when I made my videos, they could tune in and see how far along I was on their project and see each step along the way.”
Ratliff made those videos every single week for four years. Now he uses the channel to highlight unique creations he has for sale and connect with his beloved music industry.
1,280 mandolins and counting
Since 2001, Ratliff Mandolins has been a one-man show. Ratliff has cut back his batches to five mandolins at a time to ensure the utmost quality in his products now that he is the one making them entirely. His sales are done primarily through music stores or private orders. On average, he handmakes around 20 mandolins each year — with his best record being 28 in a year.
Over the past four decades, Ratliff has made 1,280 mandolins, more than 200 dulcimers, six guitars and a couple of violins. Many you will find here in the U.S., but some are being strummed across the world as Ratliff has shipped mandolins to Europe, Australia, Japan and South America. Some of those instruments were even made from lumber he cut down himself out of his own yard.
“It is indescribable that feeling you get when you play something and can remember when what you put into it was standing there in your yard,” Ratliff said with a smile.
“Even after all this time, when I put strings on (a mandolin) and play that first tune, it is still a pretty cool feeling that I never want to forget and always want to share.”
— Audey Ratliff
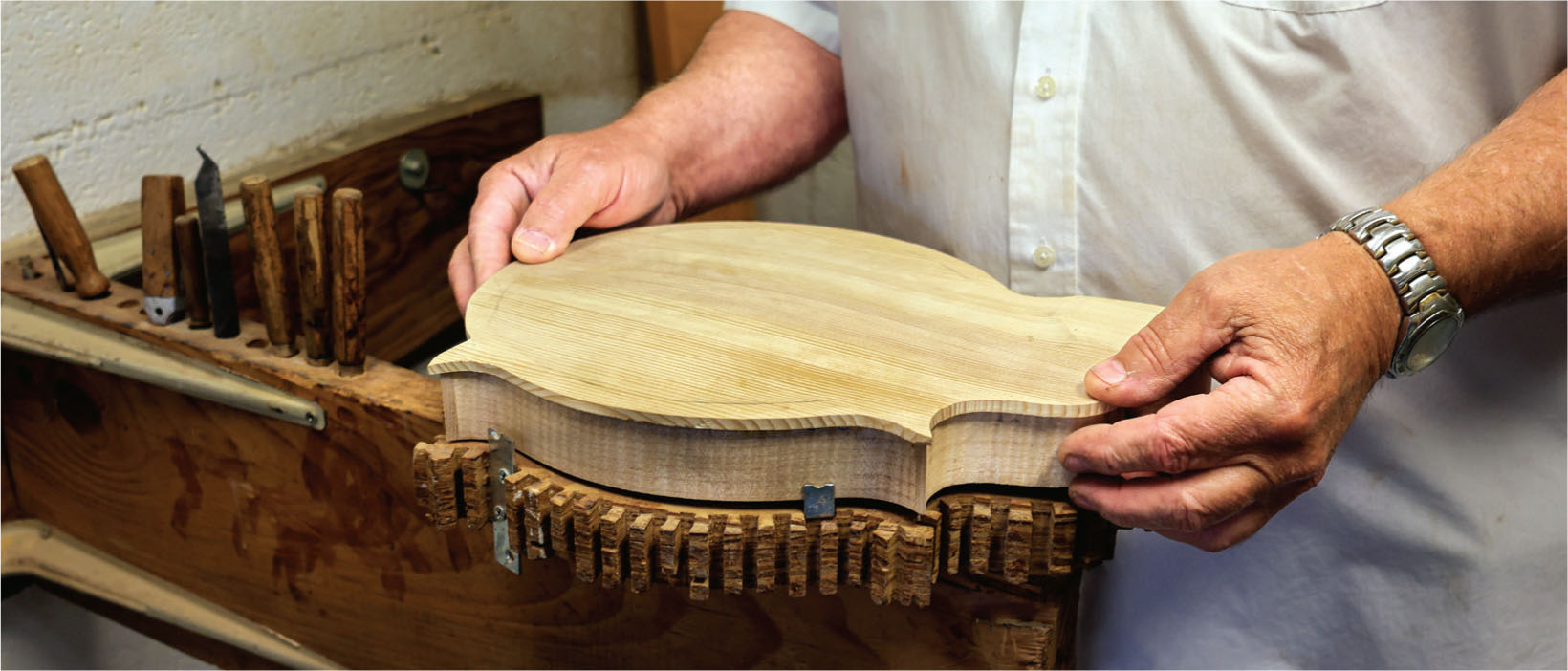